Five Tips to Keep your Workforce and Customers Safe When Using Disinfectants
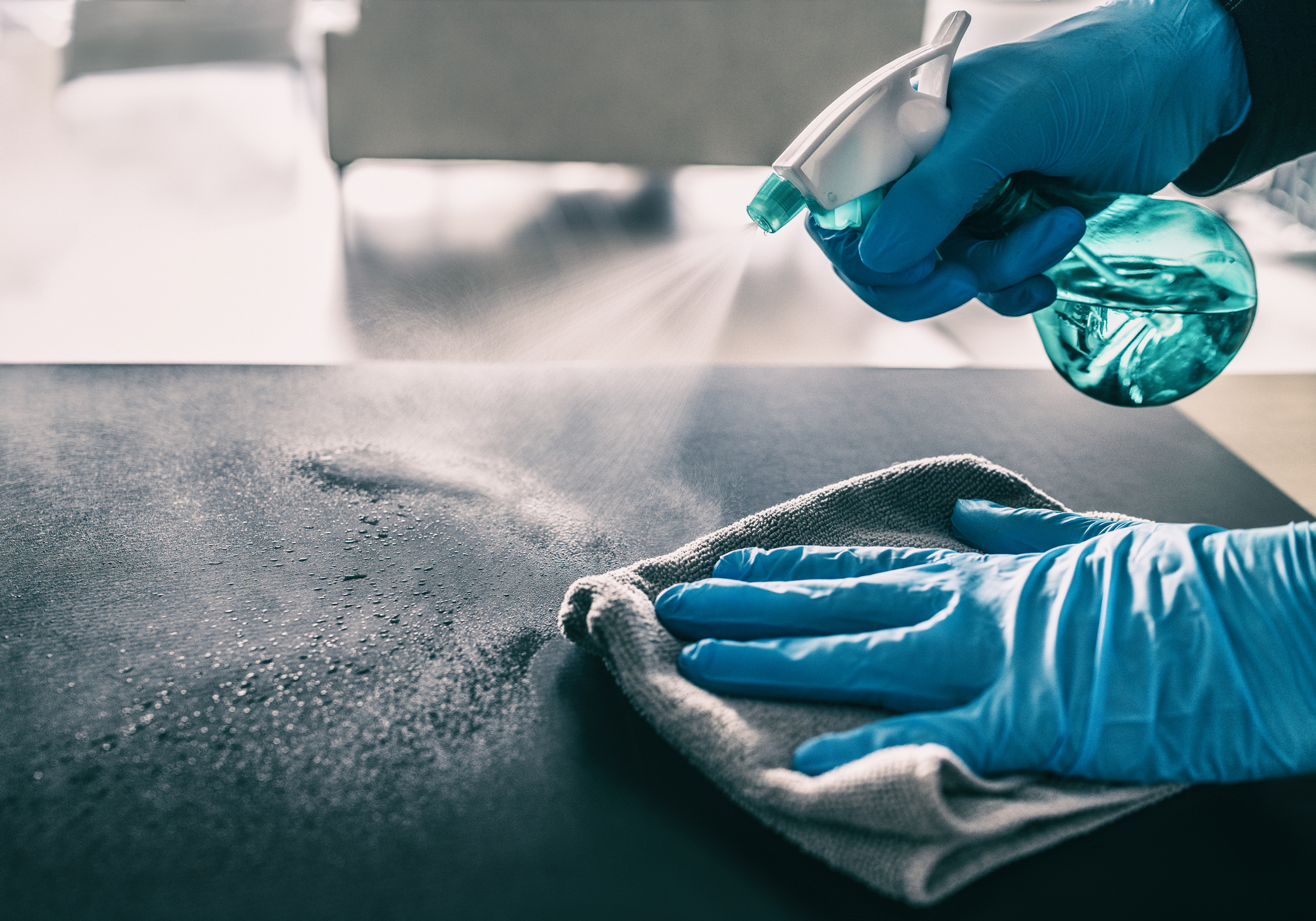
Originally published on WorkersCompensation.com | April 7, 2020
No longer exclusive to healthcare, regularly disinfecting surfaces has become a way of doing business during COVID-19. For essential services, it represents a commitment to both workforce and customers alike. It is important to note that, much like any chemical, disinfectants come with risks, and those risks compound with increased use. Here are some important safety tips to follow while using disinfectants.
1. Choose a disinfectant from the EPA’s List N: Disinfectants for Use against SARS-CoV-2.
The EPA has tested List N disinfectants to meet two criteria. First, disinfectants must show efficacy against harder-to-kill pathogens and coronaviruses similar to SARs-CoV-2 (the cause of COVID-19). Second, they must qualify for the emerging viral pathogens claim. The EPA can certify select disinfectants for use against novel pathogens after having cleared a two-stage review.
View the EPA’s full List N here: https://www.epa.gov/pesticide-registration/list-n-disinfectants-use-against-sars-cov-2
2. Never mix disinfectants, especially bleach.
Mixing disinfectants does not improve their performance or make them intrinsically safer. In fact, these mixtures can often result in conditions that are immediately dangerous to life and health for both workforce and customers. For instance, mixing bleach with other common disinfectants, such as quaternary ammonium (quat) or cleaning acids (citric or peroxyacetic), can generate toxic chlorine or chloramine gases. Hydrogen peroxide and bleach mixtures can result in explosion, if near an ignition source. Allow a bleach-cleaned surface time to completely dry before using another disinfectant or cleaning agent.
3. Disinfect electronics using 70% isopropyl alcohol (IPA) wipes.
Regularly disinfect high-touch electronics surfaces such as touch screens, phones, ATMs, keyboards and remotes. IPA safely disinfects these devices without compromising oleophobic coatings or damaging circuitry.
4. Baring allergies, use disposable nitrile gloves over latex or vinyl when disinfecting.
Nitrile gloves tend to be more chemically resistant than the latter and tend to result in fewer allergic sensitivities.
5. Discourage workers from “watering down” or “topping off” disinfectant bottles to stretch supply.
These practices can drastically reduce the efficacy of disinfectants and introduce the risk of mixing incompatible chemicals.
There is no end in sight for this increased disinfectant use, so it is important to communicate these safety tips clearly to your entire workforce. Create an integrated approach with all unit managers to help incorporate these safety measures and enforce them throughout the organization. Risk management is, ultimately, everybody’s job.