
1st Place:
Berry Global
Adding radar technology capable of detecting human motion inside of an industrial robot cell, preventing dangerous machine restarts.
The problem:
Berry Global is a leading manufacturer of plastic packaging and engineered products, focusing on sustainable innovation and design. Part of their operations involves the use of industrial robot cells, which include a closed workspace with a robot to increase production efficiency and safety. The existing administrative control of a trap key allows an operator to enter the cell, but incidents of a machine restart, while an employee is present in the hazardous area, can result in significant injury.
The solution:
Berry Global will implement radar sensors to develop a restart prevention system within an industrial robot cell. These sensors are capable of detecting human motion in a three-dimensional space, but ignore changes in surroundings, like boxes or products in the cell, that have historically led to frustrations and false alarms. The radar sensor-engineered control, in addition to existing administrative controls, dramatically lowers the possibility of an operator restarting the cell while a teammate is present in the hazardous area. This solution protects the 106 employees at the site and can generate an average savings of $25,000 per incident.
2nd Place:
Bigge Group
Installation of an environmental monitoring system to track temperature, humidity, and heat index to mitigate heat-related illness.
The problem:
Founded in 1916 and headquartered in California, Bigge Crane and Rigging Co. is a prominent provider of crane rental services, catering to commercial, government, and industrial markets. Due to the nature of their work, their employees are often exposed to high temperatures, making heat-related illnesses a significant concern. While there are manual temperature checks, there is a risk of human error, such as forgetting to record a reading, misplacing a log, or misinterpreting data.
The solution:
Deploying an enterprise-grade system with sensors connected to a real-time monitoring platform, Bigge will be able to track temperature, humidity, and heat index, enhancing safety and compliance. When predefined thresholds are exceeded, the system will automatically notify the relevant foreman or supervisor via text or email, prompting appropriate actions. Protecting 400 employees, this technology has the potential to save up to $200,000 in workers’ compensation claims costs.
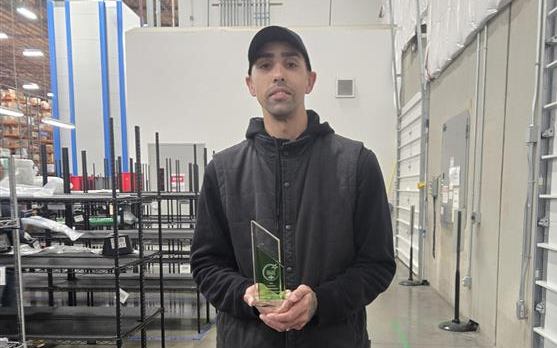
3rd Place:
Lam Research
Implementation of ergonomic equipment to reduce manual material handling tasks and improve warehouse ergonomics.
The problem:
Lam Research is a global company that designs and manufactures equipment used in the production of semiconductors, which are essential components in electronic devices. With facilities in countries worldwide, the company’s operations consists of problematic manual material handling tasks, which can result in lost work days due to sprains and strains.
The solution:
To eliminate as many compromising ergonomic positions as possible in their daily operations, Lam Research purchased two fully-powered Joe Stackers, two ErgoPack auto banders, and over 30 pneumatic and electric adjustable tables. Now that machines are doing the heavy lifting, Lam Research has seen fewer incident investigations, fewer lost workdays due to strains and sprains, and fewer recordable incidents.