
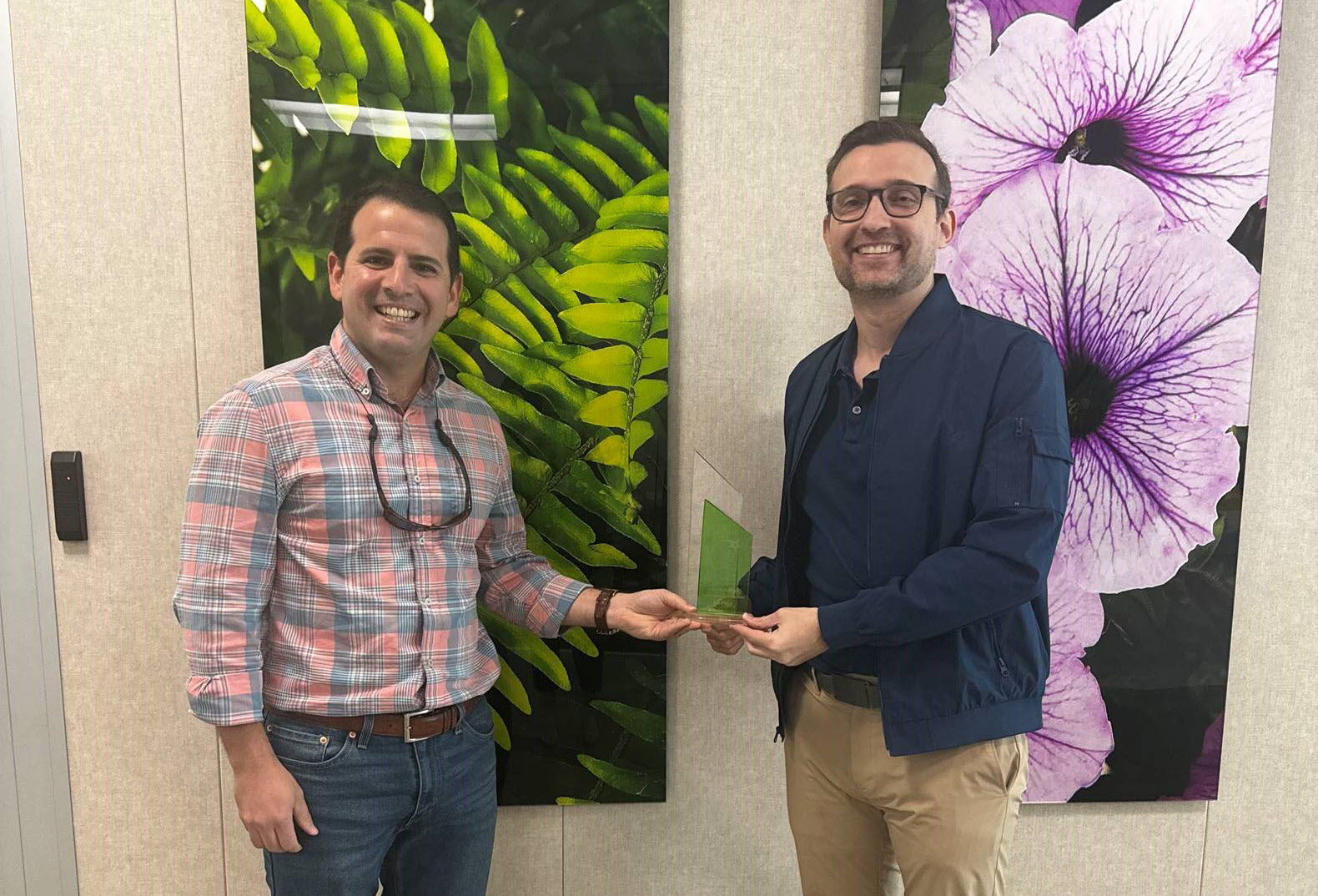
1st Place:
Costa Farms
Adding Harvesting Robots to Efficiently Mobilize Plants in the Field
The problem:
Headquartered in Miami, Florida, Costa Farms is one of the largest horticultural growers in the world, producing house plants for major retailers such as Lowe’s, Home Depot, and Walmart. Much of their operations involve tasks in the field, such as pulling, spacing, and moving plants, which are performed in ground bays. The nature of these tasks has led to many slip and fall and ergonomic-related incidents, requiring an innovative intervention.
The solution:
In keeping with their vision of prioritizing safety through automation and process development, the team implemented harvesting robots to help mobilize plants in the field in a safe and efficient manner. These robots will reduce the number of employees needed to perform the spacing tasks. The group has already seen a 50% reduction in slip, trip, and fall incidents and a 30% reduction in ergonomic incidents compared to 2022, with an estimated savings of $9,000 between the third and fourth quarters of 2023.
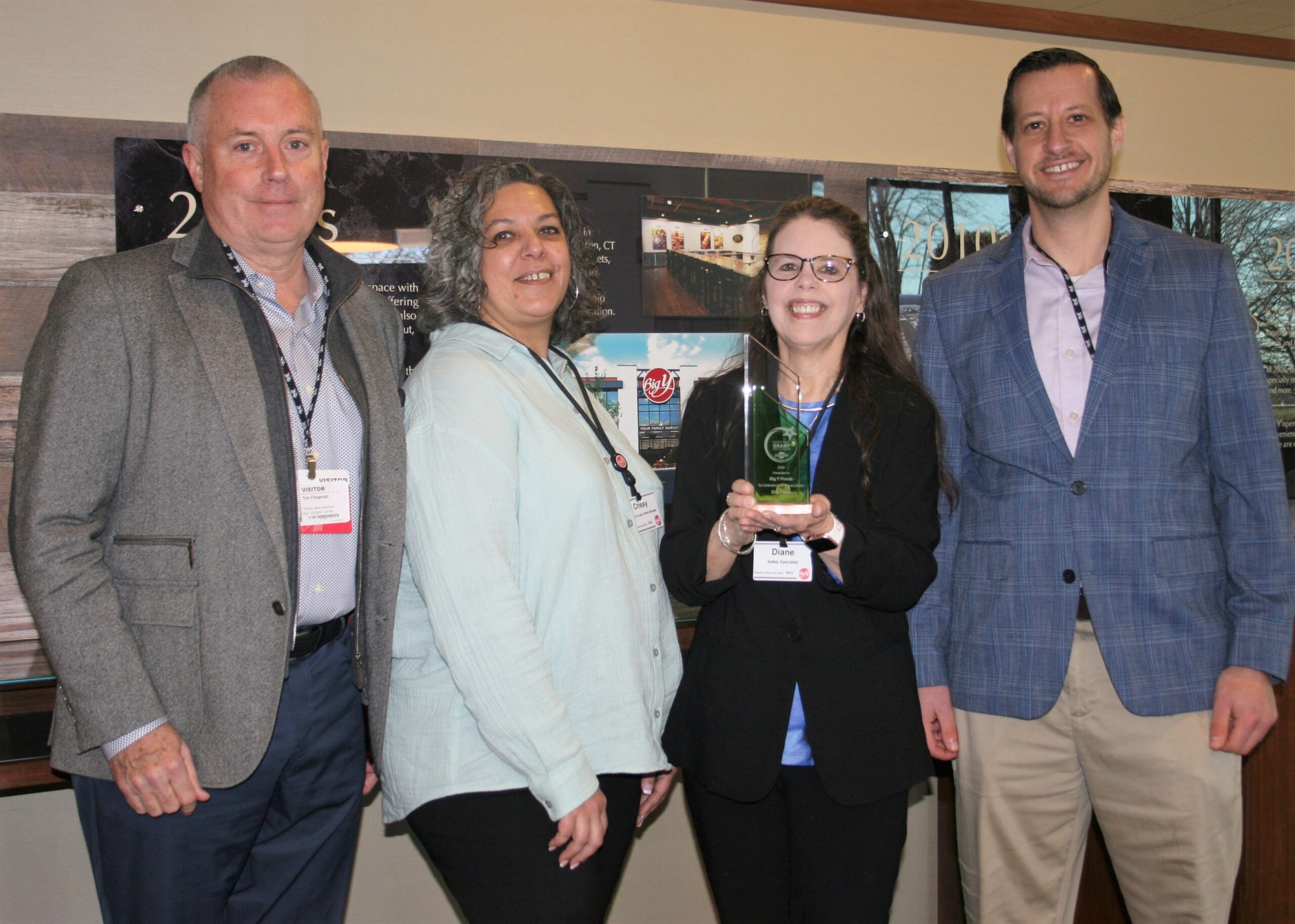
2nd Place:
Big Y Foods
Implementing Ergonomic Mixing Tables to Offset Manual Material Handling of Baked Goods
The problem:
Big Y Foods, Inc. is a regional grocery retailer with approximately 10,000 employees operating in 90 locations throughout Massachusetts and Connecticut, including a 500,000 square foot distribution center. Based on historical data from the last three years, the organization’s bakery department has incurred a yearly average claims cost of $120,000, with predominantly shoulder and back injuries. After a recent focus on ergonomics for the department, it was discovered that the height of some of the workstations, particularly for their cake decorators, was less than ideal, due to varying heights of employees and the cake being decorated. The weight of the mixer used for frosting also created a dangerous lifting exposure.
The solution:
Along with ergonomic training, the team will implement mobile, stainless steel lift tables that are adjustable from 11 to 35 inches in height and have a list capacity of 660 pounds. Operated by a foot pump, the versatility of the equipment allows for a means to move heavier items within the department, eliminating a manual material handling exposure. Costing $2,000, or 1.5% of the cost of a claim, the group anticipates a 20-30% reduction in overall incidents in the next two years.
3rd Place:
Berry Global
Developing an Engineering Solution to Eliminate Dangerous Operations of Turret Winders
The problem:
Berry Global is a leading manufacturer of plastic packaging and engineered products, focusing on sustainable innovation and design. Part of their operations involves a fleet of over 300 turret winders, built between 1970 and 2023. These machines rely on administrative controls to protect operators who are tasked with unloading finished good film rolls and replenishing empty cores. With approximately 600 employees exposed to the risk of contact with these machines, the team has recognized numerous severe injuries.
The solution:
Without a safer winder on the market, the organization has developed an engineered solution, including a set of light curtains, mechanical hard guarding, and related controls that can be retrofitted to all models of winder equipment. This solution protects the operator from the risk of turret rotation, cut over, and inbound spindle rotation. The expected incident cost reduction is $380,000 annually. Berry Global also plans to work with a major winder supplier to develop a safer winder for the industry.